The figure below describes the BOM (Bill of Materials) for product A. The MPS (Material requirements Planning) begin row in the master production schedule for product A calls for 50 units in week 2, 65 units in week 5, and 80 units in week 8. Item C is generated to make A and to meet the forecasted demand for replacement parts. Past replacement part demand has been 20 units per week (add 20 units to C’s gross requirements). The lead times for items F and C are 1 week, and for the other items the lead time is 2 weeks. No safety stock is needed for items B, C, D, E and F. The L4L lot-sizing rule is employed for items B and F; the POQ (Periodic Order Quantity) lot-sizing rule (P = 3) is used for C. Item E has an FOQ (Fixed Order Quantity) of 600 units and D has an FOQ of 250 units. On-hand inventories are 50 units of B, 50 units of C, 120 units of D, 70 units of E, and 250 units of F. Item B has a scheduled receipt of 50 units in week 2. Make a material requirements plan for the next 8 weeks for items B, C, D, E and F.
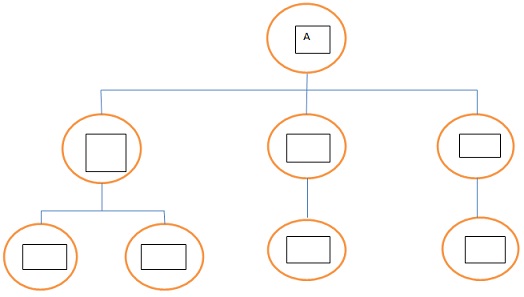